以一種基于三坐標(biāo)并聯(lián)動(dòng)力頭的五軸聯(lián)動(dòng)機(jī)床為研究對(duì)象,通過矢量鏈方法建立機(jī)構(gòu)從工作空間到關(guān)節(jié)空間的運(yùn)動(dòng)學(xué)模型,基于 Turbo PMAC 控制器設(shè)計(jì)運(yùn)動(dòng)控制需要的的硬件平臺(tái),在 LabVIEW 開發(fā)環(huán)境下基于 ActiveX 技術(shù)開 發(fā)軟件平臺(tái),采用驅(qū)動(dòng)器增益自整定結(jié)合控制器的 PID 及運(yùn)動(dòng)學(xué)前饋方法進(jìn)行伺服驅(qū)動(dòng)控制,針對(duì)并聯(lián)機(jī)構(gòu)運(yùn)動(dòng)學(xué)特點(diǎn), 在控制器內(nèi)嵌入運(yùn)動(dòng)學(xué)算法,經(jīng)過工作空間和關(guān)節(jié)空間二次插補(bǔ)的方式進(jìn)行軌跡控制,最后通過五軸加工實(shí)驗(yàn)檢測(cè)伺服驅(qū)動(dòng)控制和軌跡控制的有效性。
由于傳統(tǒng)串 聯(lián)機(jī)構(gòu)的多 軸聯(lián)動(dòng)軸機(jī) 床部件誤差累計(jì)效應(yīng)等缺點(diǎn), 難以滿足加工大型結(jié)構(gòu)件的高速、高精度要求,德國(guó)系統(tǒng)集成制造商 DST 公司開發(fā)的三坐標(biāo)并聯(lián)動(dòng)力頭———Sprint Z3 很好地解決了該問題。天津大學(xué)黃田教授根據(jù)國(guó)內(nèi)飛機(jī)制造業(yè)應(yīng) 用需求發(fā)明了 A3 并聯(lián)動(dòng)力頭及以其為核心構(gòu)件的五軸聯(lián)動(dòng)混聯(lián)裝備[1]。
隨著計(jì)算機(jī)技術(shù)飛速發(fā)展,針對(duì)多軸聯(lián)動(dòng)機(jī)床運(yùn)動(dòng)的控制技術(shù)也隨之發(fā)生了巨大變化,眾多廠商紛紛推出一系列的運(yùn)動(dòng)控制產(chǎn)品,這些運(yùn)動(dòng)控制產(chǎn)品支持通用的計(jì)算機(jī)總線,提供功能豐富的庫(kù)函數(shù),集成高速伺服插補(bǔ)和伺服濾波控制,可以滿足不同層次用戶需求[2]。
多軸聯(lián)動(dòng)的加工精度及生產(chǎn)率與其運(yùn)動(dòng)控制的品質(zhì)密切相關(guān),運(yùn)動(dòng)控制一般需要綜合考慮運(yùn)動(dòng)學(xué)算法、伺服驅(qū)動(dòng)控制、軌跡控制等諸多方面。并聯(lián)機(jī)構(gòu)由于其運(yùn)動(dòng)學(xué)耦合特性需要復(fù)雜的運(yùn)動(dòng)學(xué)算法實(shí)現(xiàn)軌跡點(diǎn)的控制。 基于數(shù)字 PID 和智能算法的伺服驅(qū)動(dòng)控制方法越來越多地被運(yùn)用到生產(chǎn)實(shí)際中[3]。 為了避免在啟停和運(yùn)行過程中的沖擊和失步, 必須實(shí)施插補(bǔ)和加減速過渡的軌跡控制, 以此為基礎(chǔ)控制各個(gè)關(guān)節(jié)電機(jī)運(yùn)動(dòng)以實(shí)現(xiàn)要求的運(yùn)動(dòng)軌跡[4]。
文中以一種新構(gòu)型的五軸聯(lián)動(dòng)機(jī)床為研究對(duì)象,采用矢量鏈方法分析機(jī)床的運(yùn)動(dòng)學(xué)模型, 自主開發(fā)設(shè)計(jì)五軸聯(lián)動(dòng)加工的運(yùn)動(dòng)控制平臺(tái),采用驅(qū)動(dòng)器增益自整定結(jié)合控制器的 PID 及運(yùn)動(dòng)學(xué)前饋的伺服驅(qū)動(dòng)控制策略,研究針對(duì)并聯(lián)結(jié)構(gòu)的二次插補(bǔ)的軌跡控制策略,
最后通過五軸加工實(shí)驗(yàn)分析運(yùn)動(dòng)控制策略的有效性。
1 機(jī)床簡(jiǎn)介
五軸機(jī)床實(shí)體模型如圖 1 所示,由三坐標(biāo)動(dòng)力頭(如圖 2 所示 A3 頭)和 2 自由度 X/Y 平臺(tái)構(gòu)成。 A3 頭的拓?fù)漕愋蜑榫哂幸黄絼?dòng)兩轉(zhuǎn)動(dòng)的 3-RPS 并聯(lián)機(jī)構(gòu),基于該動(dòng)力頭的五軸機(jī)床適用于大型航空結(jié)構(gòu)件的高速加工[5]。圖 3 所示為基于 A3 并聯(lián)動(dòng)力頭的機(jī)床機(jī)構(gòu)簡(jiǎn)圖。其中,Ai 和 Bi(i=1,2,3)分別為各支鏈球鉸鏈和轉(zhuǎn)動(dòng)副的中心,并構(gòu)成外接圓半徑分別為 a 和 b 且形心分別為A 和 B 的正三角形。 P 表示刀具參考點(diǎn), 且有 AP⊥△A1A2A3,向量AP 的模為 e。 建立固定參考坐標(biāo)系 O-xyz和刀具連體坐標(biāo)系 P-x′y′z′,建立支鏈固定坐標(biāo)系 Bi -xi yizi 和支鏈連體坐標(biāo)系 Bi-xi′yi′zi′,xi軸與 xi′軸重合。
2 運(yùn)動(dòng)學(xué)分析
A3 頭是一種 3-RPS 型并聯(lián)機(jī)構(gòu), 其工作空間與
2 運(yùn)動(dòng)學(xué)分析
A3 頭是一種 3-RPS 型并聯(lián)機(jī)構(gòu), 其工作空間與關(guān)節(jié)空間存在非線性映射關(guān)系,工作空間粗插補(bǔ)的運(yùn)動(dòng)信息不能直接轉(zhuǎn)化為各關(guān)節(jié)電機(jī)軸的運(yùn)動(dòng), 需要經(jīng)過非線性運(yùn)動(dòng)學(xué)逆解運(yùn)算[6]。設(shè)工作空間 五坐標(biāo)的 位 置 信 息 分 別 為 x,y,z,α,β,其中 α,β 是機(jī)床的兩個(gè)擺動(dòng)角。 位置逆解是將其轉(zhuǎn)化為各驅(qū)動(dòng)電機(jī)的驅(qū)動(dòng)位移。由刀具姿態(tài)角信息將刀具連體坐標(biāo)系 P-x′y′z′相對(duì)于固定參考系 O-xyz 的姿態(tài)矩陣表示為:R=Rot(y,βRot(x,α)(1)姿態(tài)矩陣還可以由歐拉角變換表示:
R=Rot(z,ψ)Rot(x,θ)Rot(z,準(zhǔn))
(2)
式中:ψ,θ,準(zhǔn)———進(jìn)動(dòng)角、章動(dòng)角和自旋角。聯(lián)立式(1)和式(2)即可求出 ψ 和 θ。設(shè)刀具參考點(diǎn) P 相對(duì)于固定坐標(biāo)系 O-xyz 的位置rP=(xP yP zP)T,顯然 zP=z。 對(duì)于 3-RPS 機(jī)構(gòu),當(dāng)已知?jiǎng)?/span>平臺(tái) ψ,θ 和 zP 三個(gè)參數(shù)時(shí),依據(jù)連帶運(yùn)動(dòng)分析[7],即可
求出 xP,yP 和 準(zhǔn)。
如圖 3 所示, 刀具參考點(diǎn) P 在固定坐標(biāo)系中的位置矢量 rP 可通過閉環(huán)矢量鏈表示:
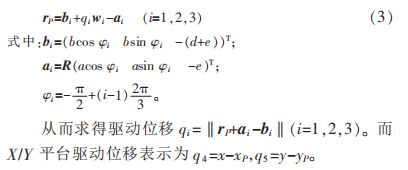
對(duì)式(3)關(guān)于時(shí)間求 1 階導(dǎo)數(shù),建立驅(qū)動(dòng)關(guān)節(jié)速度與加工軌跡速度信息的映射關(guān)系, 并用相同方法建立加速度的映射關(guān)系。
3 運(yùn)動(dòng)控制平臺(tái)設(shè)計(jì)
3.1 硬件平臺(tái)設(shè)計(jì)
以 “工 業(yè) 控 制 計(jì) 算 機(jī)+可編程 多 軸 運(yùn) 動(dòng) 控 制 器(Turbo PMAC)”的開放式結(jié)構(gòu)為核心,采用 標(biāo)準(zhǔn)化總線技術(shù)搭建的五軸聯(lián)動(dòng)機(jī)床運(yùn)動(dòng)控制的硬件平臺(tái)如圖4 所示,工控機(jī)和可編程多軸運(yùn)動(dòng)控制器通過 PCI 總線相連接,構(gòu)成雙 CPU 的實(shí)時(shí)、多任務(wù)主從控制結(jié)構(gòu)[1]。
機(jī)床硬件平臺(tái)主要包括伺服驅(qū)動(dòng)系統(tǒng)和 PLC 系統(tǒng)(數(shù)字 I/O 量控制系統(tǒng))。 伺服驅(qū)動(dòng)通過 Turbo PMAC的伺服接口通道實(shí)現(xiàn)五軸聯(lián)動(dòng),PLC 系統(tǒng)采用后臺(tái)程序監(jiān)控掃描 I/O 接口的電平變化,實(shí)現(xiàn)操作面板響應(yīng)、設(shè)備啟停、行程限位等邏輯量的控制。
3.2 軟件平臺(tái)設(shè)計(jì)
為實(shí)現(xiàn)對(duì)五軸聯(lián)動(dòng)軌跡控制、 硬件監(jiān)控和數(shù)據(jù)采集,需要建立上位機(jī)(工控機(jī))與運(yùn)動(dòng)控制器之間的通訊聯(lián)系和人機(jī)交互操作。
在 LabVIEW 開發(fā)環(huán)境下, 通過調(diào)用 Turbo PMAC的庫(kù)文件, 采用 ActiveX 引用節(jié)點(diǎn)實(shí)時(shí)控制機(jī)床的單步、點(diǎn)動(dòng)、中斷等交互式運(yùn)行操作如圖 5 所示。
利用 LabVIEW 面向?qū)ο缶幊痰撵`活性,實(shí)現(xiàn)針對(duì)五軸加工代碼語(yǔ)法檢測(cè)、安全檢測(cè)、離線仿真等作用,圖 6 為 NC 代碼編譯的后臺(tái)程序。 在 LabVIEW 開發(fā)環(huán)境下開發(fā)出如圖 7 所示針對(duì)五軸加工的數(shù)控系統(tǒng)人機(jī)交互界面,實(shí)時(shí)采集電機(jī)的運(yùn)動(dòng)信息,監(jiān)控電機(jī)運(yùn)行,從而構(gòu)建運(yùn)動(dòng)控制需要的軟件平臺(tái)。
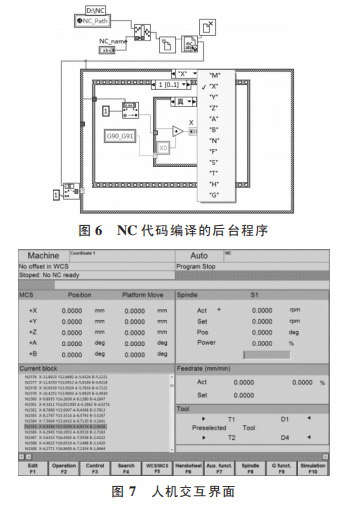
4 運(yùn)動(dòng)控制策略研究
4.1 伺服驅(qū)動(dòng)控制
文中所述五軸聯(lián)動(dòng)機(jī)床采用美國(guó) DELTA TAO 公司的 Turbo PAMC PCI型控制器和日本三菱公司的MR-J2S-A 型驅(qū)動(dòng)器。圖 8 所示為五軸聯(lián)動(dòng)機(jī)床伺服電機(jī)的 PID 控制實(shí)現(xiàn)過程,Turbo PMAC 控制器中的伺服算法采用 PID+速度/加速度前饋+陷波濾波的控制算法,驅(qū)動(dòng)器負(fù)責(zé)接收模擬量速度指令,根據(jù)實(shí)時(shí)負(fù)載變化進(jìn)行增益控制調(diào)整電流環(huán)的力矩輸出指令。 該過程的實(shí)現(xiàn)需要進(jìn)行驅(qū)動(dòng)器參數(shù)配置、控制器 PID 參數(shù)整定、控制器前饋參數(shù)整定 3 個(gè)步驟。

如圖 9 所示,將驅(qū)動(dòng)器置于速度控制模式,選擇自動(dòng)調(diào)整響應(yīng)方式,同時(shí)通過試運(yùn)行獲取機(jī)械共振頻率,根據(jù)機(jī)械共振頻率預(yù)設(shè)響應(yīng)速度,建立用于負(fù)載慣量比推算的增益表。
PID 三個(gè)基本參數(shù)通過階躍響應(yīng)進(jìn)行整定, 通常階躍響應(yīng)的位置階躍值為電機(jī)的1/4~1/2 轉(zhuǎn) ,TurboPMAC伺服參數(shù)整定界面如圖 10 所示。
4.2 軌跡控制
五軸聯(lián)動(dòng)軌跡控制的目的是在滿足精度情況下采用小段直線或圓弧去擬合工件的輪廓, 這種擬合的方法就是插補(bǔ),實(shí)質(zhì)是數(shù)據(jù)密化過程[10]。
由于并聯(lián)機(jī)構(gòu)刀具在操作空間中的運(yùn)動(dòng)是關(guān)節(jié)空間伺服電機(jī)運(yùn)動(dòng)的非線性映射(虛實(shí)映射),首先根據(jù)精度要求及插補(bǔ)周期在操作空間中離散刀具軌跡,然后通過虛實(shí)變換將數(shù)據(jù)轉(zhuǎn)化到關(guān)節(jié)空間, 再送入控制器進(jìn)行精插補(bǔ),進(jìn)而驅(qū)動(dòng)平臺(tái)運(yùn)動(dòng)。 圖 12 為二次插補(bǔ)原理圖[4]。
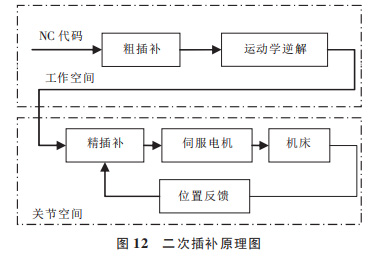
Turbo PMAC 進(jìn)行粗插補(bǔ)時(shí)將給定的 NC 代碼軌跡按時(shí)間進(jìn)行細(xì)分,粗插補(bǔ)根據(jù) NC 代碼的模態(tài)選擇直線或圓弧插補(bǔ)方式,分段時(shí)間(粗插補(bǔ)周期)由專門的變量設(shè)置, 為避免運(yùn)動(dòng)軌跡混合 時(shí)的加速度 沖擊,采用梯形加速度規(guī)律進(jìn)行速度軌跡段的過渡,梯形加速度的勻加速運(yùn)動(dòng)時(shí)間和變加速 時(shí)間由專門變量給定,五軸加工進(jìn)行的是點(diǎn)與刀具軸線矢 量的同步插補(bǔ),當(dāng)點(diǎn)的位置保持不變時(shí),Turbo PMAC 采用預(yù)設(shè)好的默認(rèn)進(jìn)給速度。 表 1 給出了粗插補(bǔ)參數(shù)的配置。
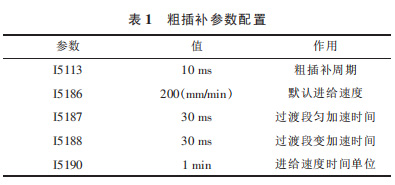
并聯(lián)機(jī)構(gòu)的關(guān)節(jié)空間伺服驅(qū)動(dòng)電機(jī)的運(yùn)動(dòng)是末端執(zhí)行器工作空間運(yùn)動(dòng)的非線性映射,Turbo PMAC 提供了嵌入式運(yùn)動(dòng)學(xué)機(jī)制,實(shí)現(xiàn)復(fù)雜的非線性運(yùn)動(dòng)學(xué)運(yùn)算。5 個(gè)電機(jī)的驅(qū)動(dòng)位移分別對(duì)應(yīng) Turbo PMAC 的全局變量 P1,P2,P3,P4,P5, 工作空間改為工作空間 x,y,z,α,β位置坐標(biāo)對(duì)應(yīng) Turbo PMAC 的坐標(biāo)變量 Q7,Q8,Q9,Q1,Q2。根據(jù)文中機(jī)構(gòu)運(yùn)動(dòng)學(xué)逆解分析,嵌入式運(yùn)動(dòng)學(xué)逆解可表示為:
精插補(bǔ)依靠 Turbo PMAC 控制卡的 3 次樣條插補(bǔ)算法實(shí)現(xiàn), 將運(yùn)動(dòng)學(xué)逆解后各關(guān)節(jié)軸離散點(diǎn)序進(jìn)一步細(xì)分,形成伺服指令,并經(jīng)伺服大驅(qū)動(dòng)電機(jī)工作。
5 實(shí)驗(yàn)
為驗(yàn)證伺服電機(jī)控制參數(shù)調(diào)節(jié)的有效性和軌跡控制的精度, 需要設(shè)計(jì)五軸加工軌跡代碼實(shí)時(shí)采集電機(jī)的跟隨誤差和加速度, 用加速度檢驗(yàn)電機(jī)控制參數(shù)有效性,用跟隨誤差度量軌跡控制精度。給定如圖 13 所示控制點(diǎn)的刀具加工軌跡,加工輪廓為式(5)表示的空間橢圓曲線軌跡,刀具軸線矢量與橢圓曲線所在平面的法向量成固定角度。
通過 CAM軟件生成加工 NC 代碼導(dǎo)入自主開發(fā)的軟件平臺(tái)進(jìn)行編譯、校驗(yàn)。圖 14 為實(shí)驗(yàn)現(xiàn)場(chǎng),機(jī)床按恒定進(jìn)給速度加工, 切削件為尼龍材料的方塊, 以50ms 采樣周期實(shí)時(shí)采集電機(jī)的運(yùn)動(dòng)信息。考慮到機(jī)床并聯(lián)機(jī)構(gòu)部分(3-RPS結(jié)構(gòu))的對(duì)稱性,僅分析其中支鏈 1 電機(jī)運(yùn)動(dòng)信息。如圖 15 所示電機(jī)跟隨誤差和實(shí)際加速度信息,ε1,ε4,ε5 分別表示支鏈 1,X 平臺(tái),Y 平臺(tái)電機(jī)的跟隨誤差,θ1,θ4,θ5 分別表示 支 鏈 1,X 平臺(tái),Y 平臺(tái)電機(jī)的實(shí)際角加速度。機(jī)床各伺服電機(jī)的每圈脈沖數(shù)為 10 000,圖 15 表明在高速進(jìn)給加工時(shí),電機(jī)跟隨誤差在 4 個(gè)脈沖之內(nèi),考慮絲杠傳動(dòng)和減速比, 反應(yīng)到末端的輪廓誤差在 1 μm 之內(nèi),滿足實(shí)驗(yàn)平臺(tái)的軌跡控制精度要求。 電機(jī)實(shí)際角加速度基本控制在-50~50 rad/s2,未出現(xiàn)明顯角加速度沖擊和震蕩,實(shí)驗(yàn)數(shù)據(jù)表明伺服電機(jī)控制參數(shù)調(diào)節(jié)的有效性。
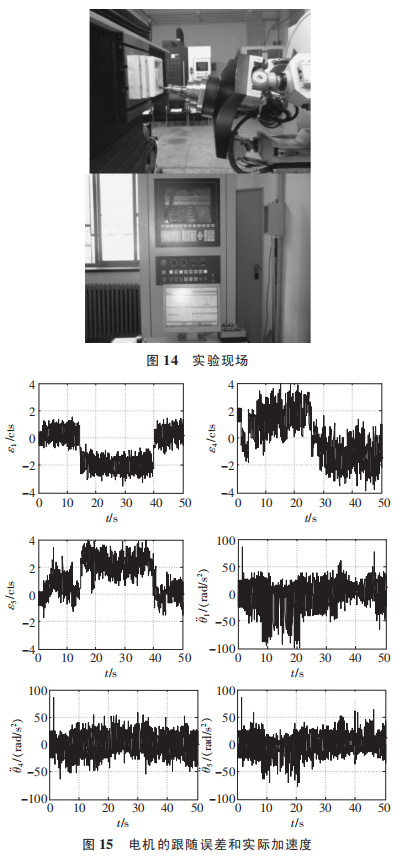
6結(jié)論
以基于 A3 頭的五軸聯(lián)動(dòng)機(jī)床為研究對(duì)象, 研究了五軸加工平臺(tái)的運(yùn)動(dòng)控制:
(1)基于矢量鏈方法分析了機(jī)床的運(yùn)動(dòng)學(xué)模型,實(shí)時(shí)的輪廓加工驗(yàn)證了運(yùn)動(dòng)學(xué)模型的準(zhǔn)確性。
(2)基于 Turbo PMAC 控制器設(shè)計(jì)了運(yùn)動(dòng)控制的硬件平臺(tái),以 LabVIEW 開發(fā)環(huán)境開發(fā)滿足五軸加工的數(shù)控系統(tǒng)人機(jī)交互界面。
(3)提出了驅(qū)動(dòng)器增益自整定結(jié)合 Turbo PMAC控制器 PID 及速度、加速度前饋的伺服驅(qū)動(dòng)控制策略,通過實(shí)驗(yàn)驗(yàn)證了伺服參數(shù)整定的有效性。
(4)開發(fā)了五軸加工平臺(tái)首先在工作空間粗插補(bǔ),然后經(jīng)過運(yùn)動(dòng)學(xué)逆解在關(guān)節(jié)空間精插補(bǔ)的二次插補(bǔ)軌跡控制策略,滿足軌跡控制精度要求。